IT Cockpit for Production Operator. Interactive platforms bolster digitization efforts in manufacturing
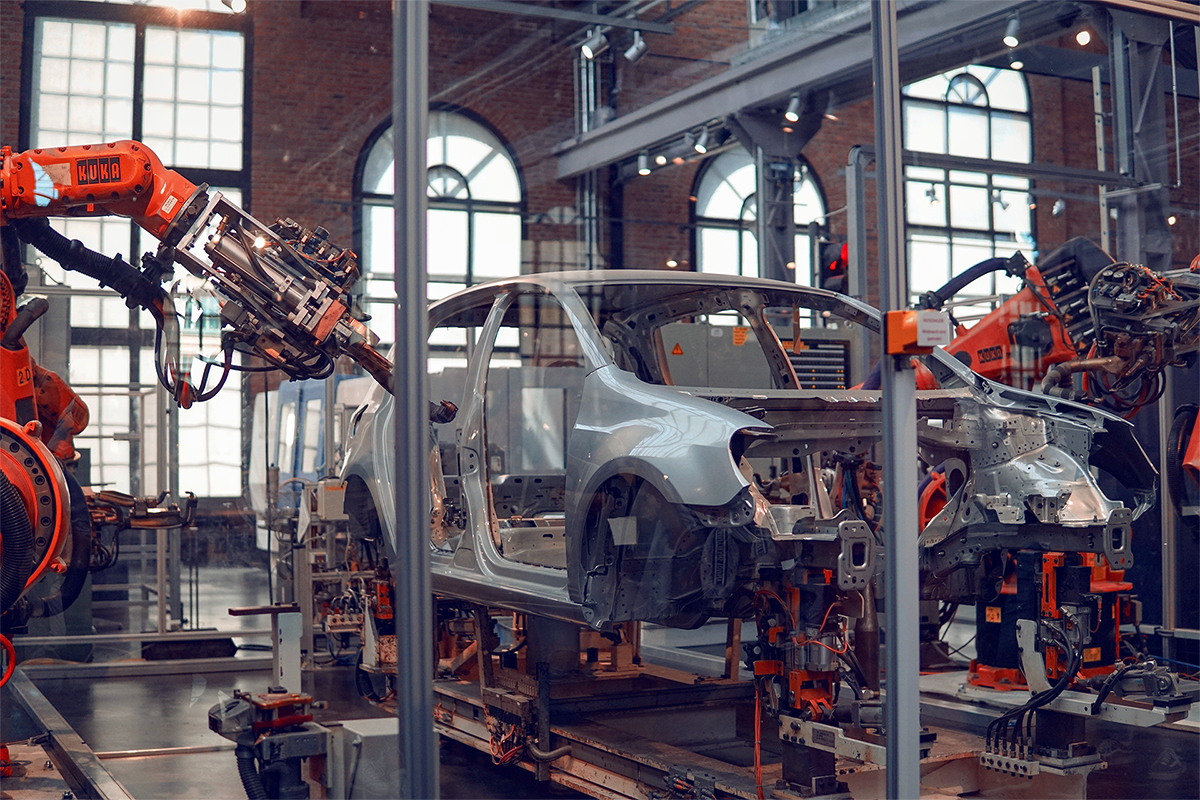
When Trask started this project in 2017, none of us foresaw that the process would take five years and that the result of the joint effort would be a fully digitalized factory floor.
What do you need to achieve such a feat? The journey starts with a sophisticated IT architecture based on microservices and event-driven patterns. It is important to abandon the traditional approach where each IT system would have its own visual interface or interactive screen. Instead, you need to create a flexible solution enabling unified interaction between people and various IT systems on a single pane of glass.
Infographic:
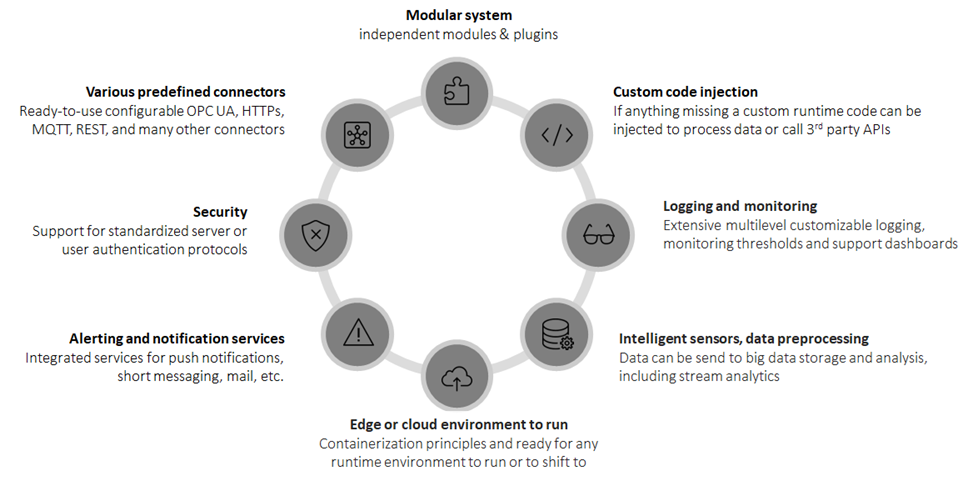
Modular and customizable
These two characteristics best describe the interactive platform that can effectively provide new capabilities to the customer – and deliver them at speed and at a reasonable cost.
Modularity means that data acquisition and processing take place outside the interactive platform. These tasks are handled by backend microservices and by long-existing IT systems that are tied to production so closely that they are virtually impossible to replace.
Our platform leverages the low-code and no-code principles to allow user-friendly customization. The solution allows SKODA AUTO to modify the appearance of individual screens. The employees can even control where each screen shows, down to the level of individual display devices along the production line.
The capabilities and benefits of our solution can be demonstrated on the onboarding of a new hire. At the start of the first shift, the supervisor will select the most appropriate screen type with additional work instructions to make it easier for the worker to handle the job. This is just one of many situations where SKODA AUTO may want to customize the appearance and content of the interactive screens. Similarly, adjustments may be needed due to parts shortages, changes in the manufacturing process, etc.

Holistic approach
The manufacturing industry has been facing a growing complexity of production combined with a shortage of skilled labor. An effective interactive visualization platform can alleviate the problems arising from this situation.
Visualization of any task should be driven by the needs of the relevant process and its support. In an effort to make the most out of the available screen area, we devised a holistic visualization concept.
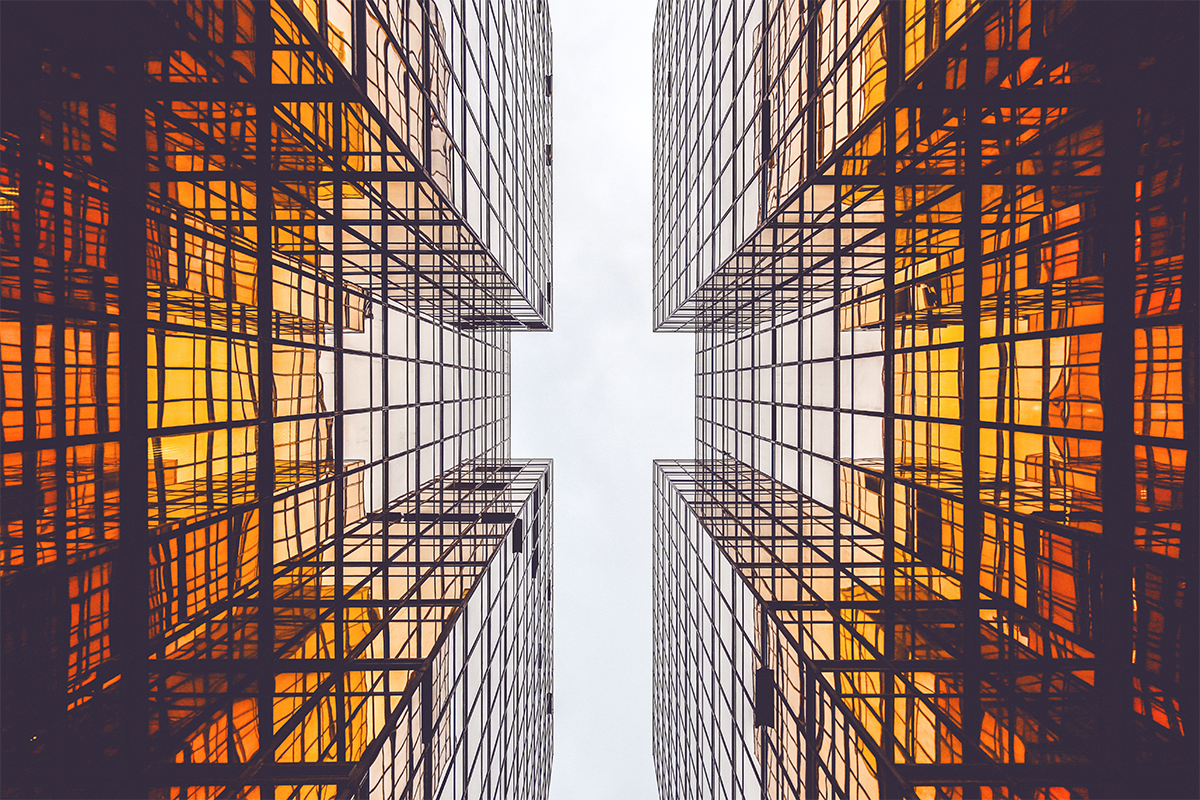
We think of the screens available to employees as a coherent way of delivering information through multiple devices to support the production process. This concept benefits considerably from the increasingly widespread usage of mobile devices, such as smartphones or smartwatches, in the production environment. While smartwatches are not very convenient to display pictorial instructions or large chunks of text, they are perfect for confirming task completion, for instance.
Employees may be given instructions on larger screens and subsequently be able to confirm the completion of their respective tasks on devices they always have at hand.
Data acquisition
Data acquisition may be a challenging task in manufacturing, as there is a wide range of various communication protocols in use. Due to the relatively long lifecycles of production lines, a single factory floor may operate different generations of technologies with different communication methods. Moreover, our customer’s policy of open competition often results in the deployment of similar technologies from different manufacturers, which does not make the situation any easier from the data acquisition perspective.
It does not make economic sense to develop special connectors for each type of communication. The ideal solution is to standardize communication from different data sources using an intermediate layer, such as Kepware. We believe that for data processing to be effective, it needs to be aggregated and categorized by product, role, workplace, etc. Our advice is therefore to abandon the notion that data should be referred to by the source – a certain system or technology.
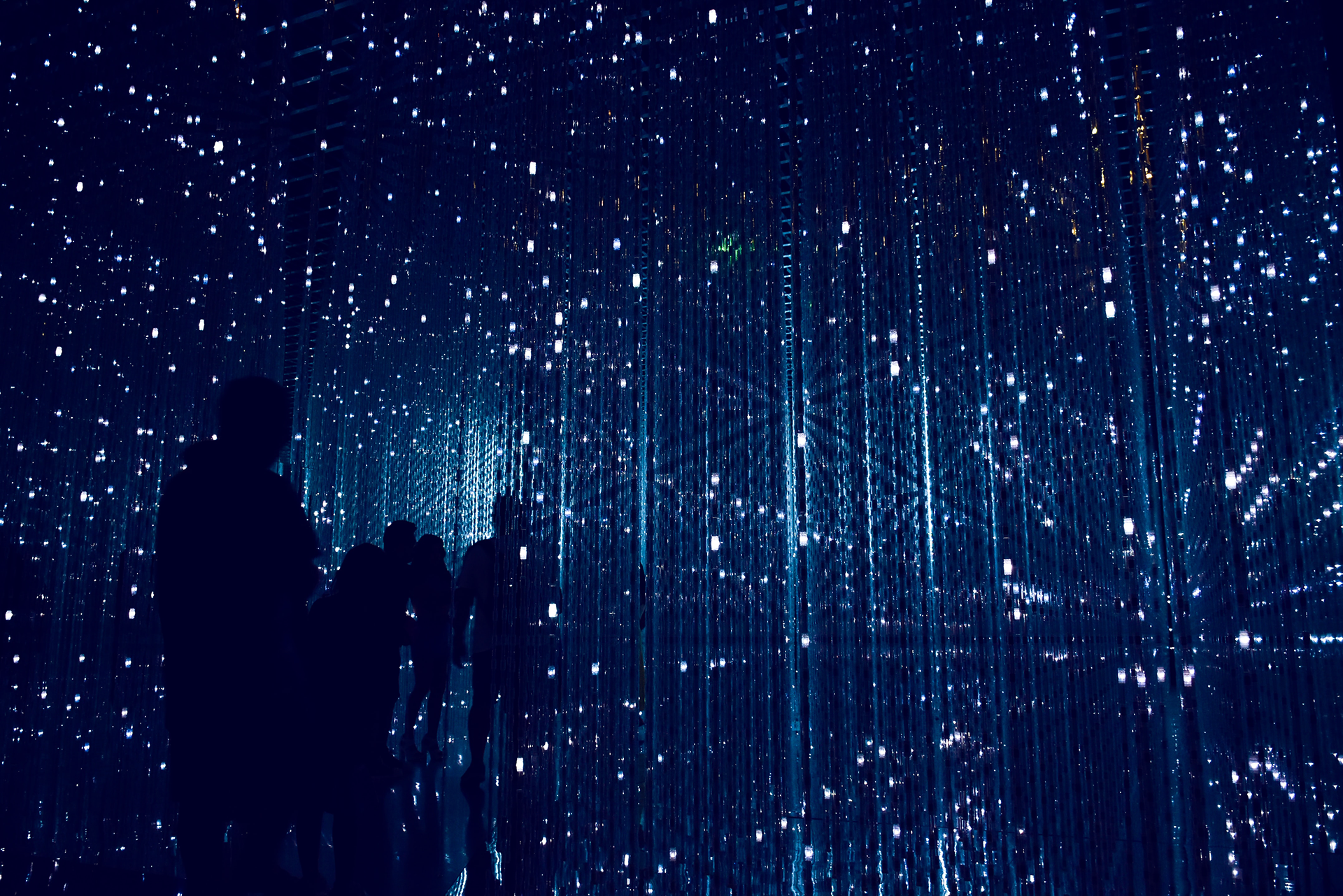
What is the biggest obstacle to digitalization?
Clearly, it is the budget.
Investments are needed to get digitalization going, but it is not the software that is the most expensive. Imagine you have a manufacturing line with 1000 employees on shift whom you want to provide all the necessary information through screens and wearable devices. Such hardware alone will require a substantial investment!
It is crucial to opt for relatively cheap devices with a sufficient level of security that can be effectively deployed on the factory floor. We worked with the local technical university to produce an IoT device with a touch display, which costs a third of the device our customer had used previously. To further simplify support of those devices in the event of failure, we created a plug & play solution. If a device malfunctions, it will be replaced with another one, which will only need to configure itself with the same IP address as the previous one. All necessary configurations are provided by the server side.
We are very happy with the solution that we have delivered, but there is always room for improvement. We are pursuing new goals, some of which are related to cloud services. Would you like to join us on this journey?
Petr Filip
Analyst, SA Production
petfilip@thetrask.com